Learn How to Conduct a Job Site Hazard Assessment
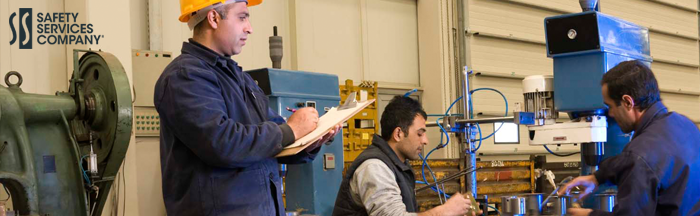
Every year, over 4 million workers are the victim of a serious injury or illness on the job. Daily, more than 12 of these injuries result in death. The majority of these injuries and deaths can be prevented if the hazards that caused them had been properly identified and controlled ahead of time. The importance of conducting a worksite hazard assessment is immense; if the tragedies caused to an employee and their family by serious injury or death isn’t reason enough, company losses as a result each year are in the billions of dollars.
A thorough hazard assessment will allow you to identify and then eliminate or control physical hazards and unsafe employee work practices before they occur. Review these five basic steps to get you started on your hazard assessment.
1. Preparation
Before you can begin the actual assessment, you’ll need to create a system of job prioritization and a ranking system for the severity of each hazard. In general, it’s most effective to begin with jobs with the highest risks, such as:- Documented to have frequently resulted in injury or illness
- Present severe and life-threatening hazards even if there is no documented instances of prior occurrences
- Undergone significant changes in procedure or equipment or are altogether new to your company
- Procedures of a nature complicated enough to require written instructions
- Involve serious and life-threatening hazards that could be triggered by a single worker error
The highest ranking of probability would include employee contact with a hazardous material or atmosphere, because an injury is nearly guaranteed. The lowest ranking would be that it is virtually impossible for injury to occur.
In terms of severity, the highest ranking may be that the injury will almost certainly cause fatality to numerous workers, and the lowest that the worst-case scenario is a minor cut or bruise.
In this way, you will be able to see a written, visual representation of what jobs and hazards will require the most highly-focused attention.
2. Job Step
Next you create your job hazard analysis. For best organization and record keeping, you should create a separate document for each individual job on the worksite. Each document should consist of three columns: Job Step, Possible Hazards, and Preventative Measures.In the Job Step column, describe each basic step of a task, from first to last. For example, if the task involves an employee receiving a shipment at the warehouse, the first step may be described:
Employee guides delivery truck to the loading dock.
Cover each individual step of the job process, including both the person involved (employee, manager, maintenance crew, etc.) as well as the action (guiding the truck, loading shipment onto pallets, etc.).
3. Possible Hazards
In the center column, describe any imaginable safety hazards associated with the job step indicated in the first column. Be thorough — where safety is concerned, leave no stone unturned.Regarding the aforementioned example, the obvious safety hazard may be that the worker is out of view of the driver and the delivery truck is backed up over them. But there are other considerations.
Is the worker guiding the truck from an elevated loading dock (is there a falling hazard?)?
Is it possible for the worker to become crushed between the truck and a nearby stationary object?
Are there clearance issues?
When identifying and documenting hazards, be complete enough in your description to answer the following questions:
- What could possibly go wrong?
- What would the result be should a worker come into contact with the hazard?
- How could the worker come into contact with the hazard?
- What other factors may contribute to the hazard?
- What is the likelihood of the hazard arising?
“If the employee is standing too close to an unprotected edge of the loading dock(1) or they are knocked over by the moving delivery truck(4), there is a high risk(5) that they may fall to the lower level(3) resulting in bodily impact injuries or death(2).”
4. Preventative Measures
In the final column, describe any possible preventative measures that could be implemented to either control or altogether eliminate the safety hazard. When considering prevention, take the three control methods into account:Engineering Controls:
Engineering controls involve physically altering equipment or environments to prevent employees from coming into contact with a hazard. In the example we’ve been using, one possibility may be to install guardrails along the leading edges of the dock where an employee would be stationed. Another idea would be to implement visual or audial indicators such as flashing lights or warning sounds to assist delivery truck drivers in backing up without the necessity of an employee being within close physical proximity.
Engineering controls are considered to be the most desirable and effective form of hazard prevention because they eliminate the hazard altogether. Engineering should always be the first step when possible.
Administrative Controls
If it is impossible to engineer a hazard out of existence or displace employees from a hazard’s exposure, the next best step would be administrative controls.
These controls involve monitoring, adjusting, or training safe work practices into employees’ job routines. An example may be that the employee uses pre-established hand signals for guiding a delivery truck driver while remaining in a designated and visible safe area.
Safety training is included as an administrative control.
Administrative controls are often thought of as only moderately effective since they rely on human behavior.
Personal Protective Equipment (PPE)
PPE should be required whenever possible, but never considered the primary defense against a safety hazard. This can include safety goggles, gloves, hard hats, back braces, face shields, chemical protection aprons, respirators, etc. For example, if the employee is exposed to exhaust fumes while guiding delivery trucks to the loading docks, requiring respirators or face masks may be desirable.
Job hazard assessments need to be thought of as a living document; they should undergo constant maintenance and upgrades as new hazards and hazard control methods are identified. Also update the assessment whenever there is a change to the work process.
Remember to be as thorough as possible — it’s much better to go overboard in describing the layout of a hazard than to overlook a crucial element.
To leave you with a final thought from a supervisory perspective:
Unfortunately, employees who have become comfortable and adept enough at performing their jobs may be inclined to implement their own ideas on safe practices. A job hazard assessment is only effective if it results in preventative actions taken, and actions taken are only guaranteed if employees are encouraged to do so with positive supervision and continuing training.